- Zement ist ein vielschichtiges Klimaproblem
- Zement-Herstellung: Temperaturen von bis zu 1.500 Grad Celsius
- Hohe Emissionen beim chemischen Prozess
- Die Feinheiten der Zementchemie
- Elektrolyse bringt den Durchbruch
- Tests mit dem Zement von Sublime
- Effizienz reicht nicht
- Anderer Ansatz für die Zement-Herstellung
- "Ein Zementwerk für Ameisen"
- "Es ist auch nicht ein 'neuer' Zement"
- Nächstes Ziel: Zehntausende Tonnen Zement pro Jahr
Statt Hitze: US-Startup entwickelt völlig neue Methode zur Zement-Herstellung
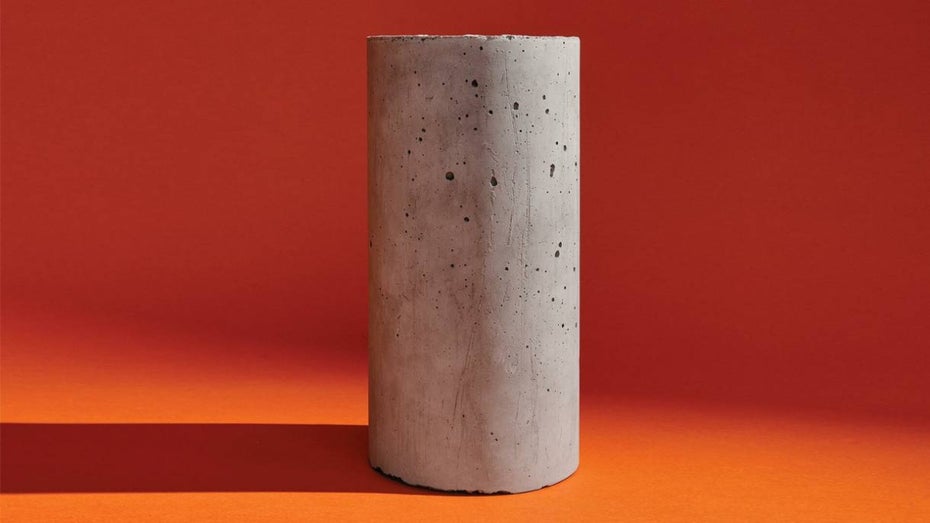
Wenn wir über das Klima sprechen, sprechen wir meist über Verkehr, Heizenergie oder Industrieemissionen. Über Zement, der in nahezu jedem Gebäude steckt oder in Bauwerken wie Dämmen, Brücken oder Tunneln, sprechen wir fast nie. Dabei ist die Zementproduktion für mehr als sieben Prozent der weltweiten Kohlendioxidemissionen verantwortlich.
Seit Tausenden von Jahren stellen die Menschen Zement in der einen oder anderen Form her. Die alten Römer verwendeten vulkanische Asche, zerstoßenen Kalk und Meerwasser, um Aquädukte und ikonische Bauwerke wie das Pantheon zu errichten. Die moderne Version des hydraulischen Zements – der durch die Reaktion mit Wasser aushärtet und anschließend wasserbeständig ist – stammt aus dem frühen 19. Jahrhundert. Er wird aus weithin verfügbaren Materialien hergestellt, ist billig und einfach zu produzieren.
Dieser Text ist zuerst in der Ausgabe 2/2024 von MIT Technology Review erschienen. Hier könnt ihr die TR 2/2024 bestellen.
Zement ist ein vielschichtiges Klimaproblem
Heute ist Zement – meist Portlandzement – mit einer Jahresproduktion von etwa vier Milliarden Tonnen einer der meistverwendeten Werkstoffe der Welt – und ein vielschichtiges Klimaproblem. Seine Herstellung ist energieintensiv: Das Innere eines herkömmlichen Zementofens muss heißer sein als die Lava eines Vulkans, um die nötigen chemischen Reaktionen in Gang zu setzen. Um diese Temperaturen zu erreichen, werden normalerweise fossile Brennstoffe verbrannt. Außerdem setzen die chemischen Reaktionen selbst große Mengen Kohlendioxid frei.
Eine Lösung für diese Klimafalle könnte durch die Rohre von Sublime Systems fließen. Das von zwei MIT-Batteriewissenschaftlern gegründete Startup entwickelt eine völlig neue Methode zur Herstellung von Zement. Statt mit Hitze arbeitet es mit Strom. Eine Pilotanlage für 100 Tonnen im Jahr zeigt bereits, dass es möglich ist, einen der wichtigsten Baustoffe der Welt elektrochemisch herzustellen.
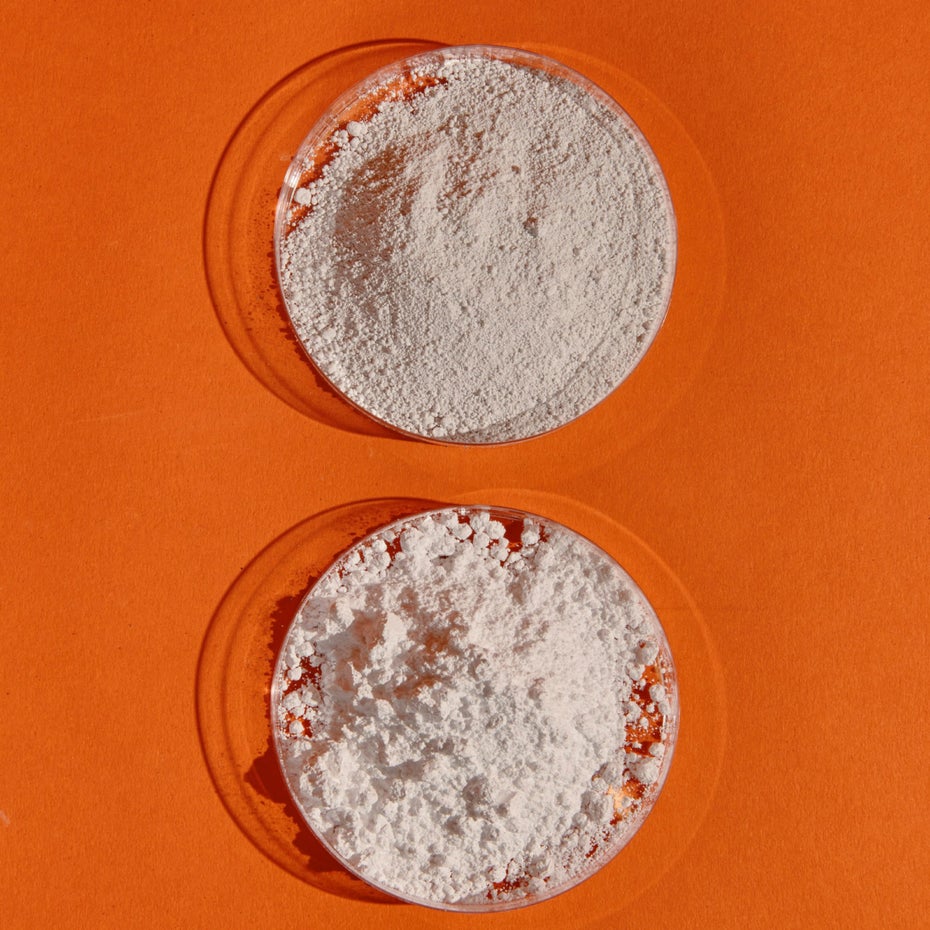
Sublime-Silikate und Sublime-Kalk, die zwei Hauptkomponenten des Zementes, unterscheiden sich optisch nicht von konventionellem Material.
(Foto: Bob O’Connor)
Das ist immer noch sehr wenig im Vergleich zu herkömmlichen Zementwerken, die jährlich eine Million Tonnen oder mehr herstellen, aber bis zum Ende dieses Jahrzehnts will es seine Jahresproduktion auf eine Million Tonnen ausweiten. Da schon konventionelle große Zementwerke über eine Milliarde US-Dollar kosten, muss Sublime schnell wachsen und gleichzeitig zusätzliche Mittel aufbringen, die dieses Wachstum finanzieren – und das für einen günstigen Massenrohstoff wie Zement. Eine weitere Herausforderung ist es, in einer Branche mit hohen Risiken und niedrigen Margen die Bauherren davon zu überzeugen, das neue Material überhaupt zu verwenden.
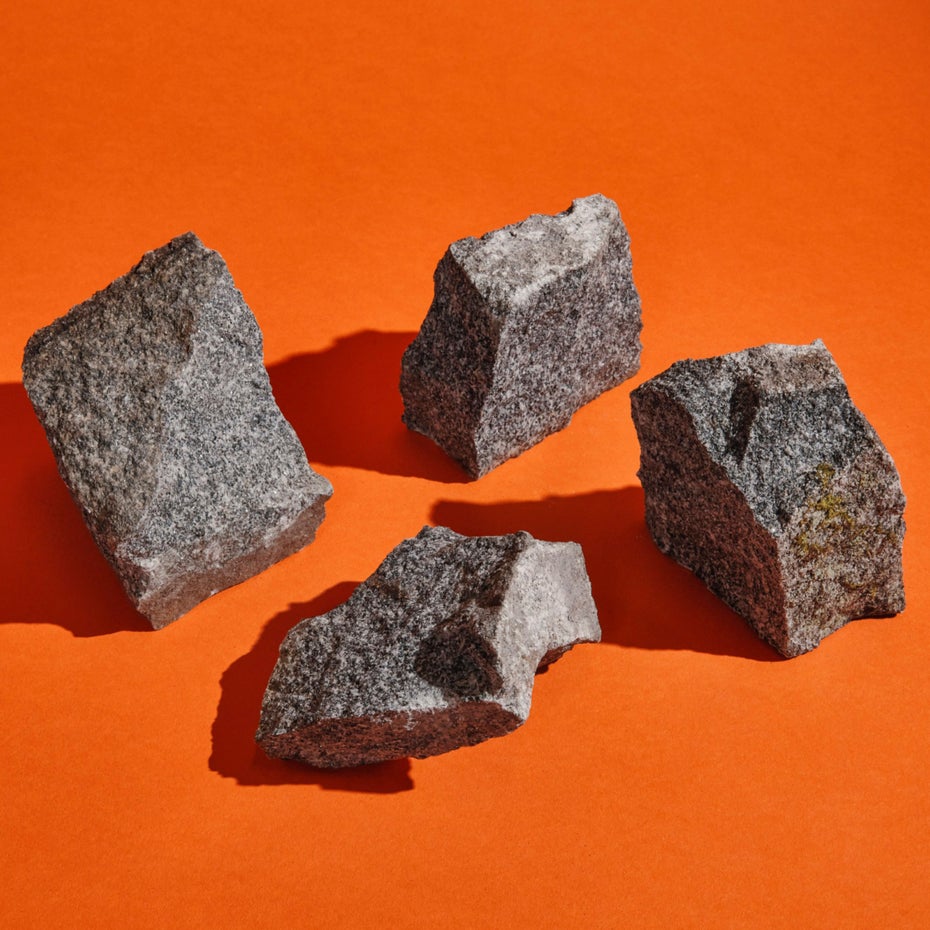
Mit dem Sublime-Verfahren kann Zement auch aus Gesteinen gewonnen werden, die kein Karbonat enthalten.
(Foto: Bob O’Connor)
Zement-Herstellung: Temperaturen von bis zu 1.500 Grad Celsius
Der Mensch verbraucht – lässt man Wasser außen vor – gewichtsmäßig von keinem Material auf der Erde so viel wie von Beton. Und Zement ist der Klebstoff, der dieses Material zusammenhält. Er macht etwa zehn Prozent seines Volumens aus.
Zur Herstellung von Zement wird heute eine Mischung aus Kalkstein, Sand und Ton gemahlen und in Öfen bei Temperaturen von bis zu 1.500 Grad Celsius gebrannt. Die Hitze setzt komplexe Reaktionen in Gang, die den Kalkstein in Kalziumoxid umwandeln und diesen mit dem Siliziumdioxid aus Sand und Ton verbinden.
Etwa 40 Prozent der mit der Zementherstellung verbundenen Treibhausgasemissionen stammen aus fossilen Brennstoffen, die nötig sind, um die für diesen Prozess nötige Wärme zu erzeugen. Dies ist ein allgemeines Problem in der Schwerindustrie: Fossile Brennstoffe haben sich aufgrund ihrer niedrigen Kosten in den Produktionsprozessen festgesetzt, sagt Rebecca Dell von der gemeinnützigen Forschungsgruppe ClimateWorks. Allerdings kommen jetzt kostengünstigere erneuerbare Energien ins Spiel, sodass mehr Industriezweige auf Strom umsteigen können.
Öfen für die Zement-Herstellung elektrisch zu betreiben, ist durchaus möglich, und einige große Unternehmen wie Cemex arbeiten daran, CO₂-Emissionen aus dem Wärmebedarf und damit die Klimaauswirkungen der Zementproduktion zu senken. Das ändert jedoch nichts an den restlichen Emissionen: Denn rund 60 Prozent entstehen nicht durch Wärme, sondern durch komplexe chemische Reaktionen, die bei der Umwandlung der Ausgangsstoffe in den Baustoff ablaufen.
Hohe Emissionen beim chemischen Prozess
Der meiste Zement wird aus Kalkstein (CaCO3) hergestellt, einem Sedimentgestein, das Kalzium, Sauerstoff und Kohlenstoff enthält. In Zementöfen wird der Kalkstein in Kalziumoxid (CaO) umgewandelt, auch gebrannter Kalk genannt – wie bei der konventionellen Zement-Herstellung. Das Endprodukt ist eine Mischung aus unterschiedlichen Silizium-, Kalzium- und Sauerstoffverbindungen, die nach dem Vermischen mit Wasser (und der Zugabe von Sand und Kies) zu Beton aushärten.
Kalkstein besteht etwa zur Hälfte aus Kohlendioxid und das wird bei der Umwandlung zu Kalziumoxid abgespalten. Entsprechend hoch sind diese Emissionen aus dem chemischen Prozess – und eine vollständige Dekarbonisierung der Zementindustrie würde eine radikalere Neuerfindung für die Zement-Herstellung erfordern. Hier kommt Sublime ins Spiel.
Die Feinheiten der Zementchemie
„Zement bekommt nicht wirklich die Aufmerksamkeit, die er meiner Meinung nach verdient“, sagt Leah Ellis, Mitbegründerin und CEO von Sublime. Sie spricht schnell, als ob ihr die Zeit davonliefe. Ihre Gedanken sprudeln nur so aus ihr heraus und werden von einem leichten kanadischen Akzent begleitet. Während sie die Feinheiten der Zementchemie erklärt, leuchten ihre Augen hinter einer kaugummirosa Brille.
Ellis hatte nicht vor, in die Baustoffbranche einzusteigen. Sie studierte bei dem berühmten Batteriepionier Jeff Dahn. Danach wechselte sie zum MIT, um mit Yet-Ming Chiang zusammenzuarbeiten, einer weiteren wichtigen Persönlichkeit in der Batterieforschung und einem Serien-Gründer. Chiang hat mehrere Unternehmen im Bereich der Energiespeicherung auf den Weg gebracht, darunter A123 Systems, 24M und Form Energy. Jetzt ist er gemeinsam mit Ellis Mitbegründer von Sublime Systems.
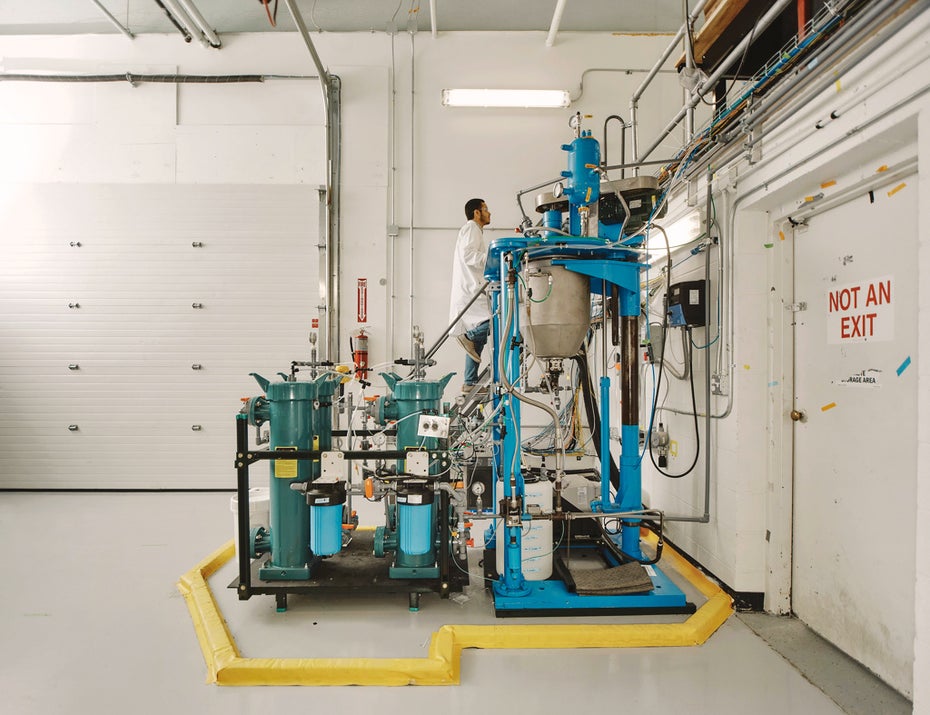
Noch stellt die Anlage Zement nur im Pilotmaßstab her. Das soll sich demnächst ändern. (Foto: Bob O’Connor)
Als Ellis am MIT ankam, führte Chiang sie in sein Büro und fragte sie, ob sie sich mit Batterien langweile. „Und ich dachte, das sei eine Fangfrage“, sagt sie, „denn er ist ja ein berühmter Batterieforscher.“ Aber hinter der Frage steckte Chiangs Idee, Zement herzustellen, indem man ein Werkzeug aus der Batterieforschung verwendet: die Elektrochemie. Statt Zementöfen mit fossilen Brennstoffen zu beheizen, glaubte Chiang, könnten sich die erforderlichen chemischen Reaktionen auch durch Strom auslösen lassen.
Elektrolyse bringt den Durchbruch
2019 entdeckten Ellis und ihre Forscherkollegen eine Methode, Chiangs Idee umzusetzen – per Elektrolyse. Normalerweise dient die Elektrolyse dazu, Wasser in Wasserstoff und Sauerstoff zu spalten. Aber auch andere Reaktionen sind mit Strom möglich. Im Tank eines Elektrolyseurs mit pH-Gradienten kann auf der sauren Seite Kalziumhydroxid (Ca(OH)2) – sogenannter Löschkalk – abgeschieden werden. Wird dieser gemeinsam mit Sand (Siliziumdioxid) gebrannt, entsteht Alit (Trikalziumsilikat, Ca3SiO5). Und das wiederum ist ein wichtiger Bestandteil des konventionellen Portlandzementes.
Nach einigen zusätzlichen technischen Entwicklungen und Branchenanalysen beschlossen Ellis und Chiang, die Forschung in ein Unternehmen mit Ellis an der Spitze auszugliedern. Chiang sagt: „Es dauerte nicht lange, bis ich erkannte, dass es sowohl eine Ausgangsidee gab als auch eine Person, die sie umsetzen konnte.“
Einige Jahre später betreibt Sublime eine Pilotproduktionslinie. Ein großer Fortschritt, bedenkt man die Anfänge am MIT, als Ellis und ihre Laborkollegen gerade genug Material für ein einziges Plättchen produzierten. Die Anlage wurde Ende 2022 in Betrieb genommen, sagt Mike Corbett, der technische Leiter von Sublime, und ist 20-mal größer als alles, was das Unternehmen im Labor betrieben hatte.
Tests mit dem Zement von Sublime
In einem riesigen Raum am Hauptsitz des Unternehmens reihen sich Edelstahltanks aneinander. In die Tanks auf der einen Seite kommt gemahlenes Gestein, aus den Tanks auf der anderen Seite kommt Löschkalk. Die Ergebnisse der verschiedenen Versuchsreihen werden in 20-Liter-Eimern gesammelt, die sich auf Metallgestellen stapeln. Der Löschkalk darin ist ein unscheinbares weißes Pulver, kreidig und leicht verklumpt wie Backpulver in einer zu lange offen gelassenen Schachtel.
Es wäre schwierig, mit dem Inhalt dieser Eimer irgendetwas zu bauen: Bei voller Kapazität würde die Pilotanlage etwa eine Woche brauchen, um genug Zement für einen einzigen Betonlaster herzustellen. Und man bräuchte drei bis vier LKW-Ladungen, um das Fundament für ein durchschnittliches Einfamilienhaus zu gießen.
Aber das ist auch gar nicht das Ziel des Unternehmens. Das Material in den Eimern geht an potenzielle Partner, dient Tests mit Zementblöcken und hilft bei der Planung der nächsten, deutlich größeren Anlagen. Diese sollen beweisen, dass das Sublime-Verfahren in der Zementindustrie funktionieren kann.
Effizienz reicht nicht
Sublime Systems sind nicht die Einzigen, die versuchen, den grauen Zement grüner zu machen. Frühe Bemühungen konzentrierten sich weitgehend auf die Effizienz konventioneller Verfahren, sagt Radhika Lalit, Industry Initiative Director bei der Climate Imperative Foundation. So können beispielsweise zementähnliche Füllstoffe die Gesamtemissionen senken, ohne die Eigenschaften des Betons zu beeinträchtigen. Diese zementähnlichen Zusatzstoffe können mit den Inhaltsstoffen im Zement reagieren.
Diese Strategie funktioniere aber nur bis zu einem bestimmten Anteil, so Lalit: Danach begännen diese Füllstoffe, die Festigkeit und Lebensdauer des Zements zu beeinträchtigen.
Anderer Ansatz für die Zement-Herstellung
Eine andere Strategie, die Auswirkungen der Zement-Herstellung auf das Klima zu verringern, verfolgt das kanadische Unternehmen CarbonCure Technologies. Es hat eine Technologie entwickelt, Kohlendioxid in Zementmischungen zu injizieren. Nach Angaben von CarbonCure kann das Gas dann mit dieser Mischung reagieren und mineralisieren. Dadurch wird es aus der Atmosphäre ferngehalten und erhöht die Festigkeit des Materials. CarbonCure arbeitet mit Unternehmen wie Heirloom Carbon Technologies zusammen, um die langfristige Speicherung von Kohlendioxid in Beton zu demonstrieren.
Die Verringerung des gesamten Materialeinsatzes oder die Zugabe von Füllstoffen können die Emissionen jedoch nicht auf null bringen. Also wollen viele etablierte Zementhersteller ihre bestehenden Anlagen mit Systemen zur Abscheidung und Sequestrierung von Kohlendioxid ergänzen, sagt Lalit. Das helfe aktiven Anlagen, ihre Emissionen zu senken, sodass sie nicht vollständig ersetzt werden müssen, um die Industrie sauberer zu machen.
Die Erweiterung der bestehenden Infrastruktur um CCS-Technologien könnte die Betriebsdauer konventioneller Zementfabriken verlängern – ein großer Vorteil für neu gebaute Anlagen, die oft für 30 bis 50 Jahre ausgelegt sind. Allerdings ist CCS in der Schwerindustrie noch weitgehend unerprobt, sagt Lalit: Oft werden nicht alle Emissionen aufgefangen, und bei den wenigen bestehenden Großanlagen kam es zu Verzögerungen.
Die Netto-Null-Ziele auf diesem Weg zu erreichen, würde den Zement ungefähr doppelt so teuer machen wie bisher, sagt Ellis. Deshalb versuchen es Sublime und eine Reihe anderer Startups mit radikaleren Methoden. Eines der am besten finanzierten Zement-Start-ups ist Brimstone aus Kalifornien. Es habe ein „kohlenstoffnegatives“ Verfahren entwickelt, das mehr Kohlendioxid aus der Atmosphäre ziehe, als es ausstoße, sagt Cody Finke, CEO von Brimstone. Dies funktioniere auf zwei Wegen: Erstens verwende man statt Kalkstein Silikatmineralien, die kein Kohlendioxid enthalten. Außerdem sei ein Abfallprodukt der Silikate ein magnesiumhaltiges Material, das wie ein Schwamm wirke, Kohlendioxid aus der Luft aufsauge und mineralisiere. Allein dies würde ausreichen, um die Emissionen aus der konventionellen Wärmeerzeugung auszugleichen, erklärt Finke. Zudem plane das Unternehmen den Einsatz von Elektroöfen. Mit Strom aus dem US-Netz betrieben, ließen sich unter dem Strich pro Tonne Zement etwa 130 Kilogramm Kohlendioxid binden.
„Ein Zementwerk für Ameisen“
Sublime hingegen wollte ursprünglich normalen Portlandzement herstellen. „Für etwas so Kostengünstiges wie Zement dachten wir, dass man das produzieren muss, was der Markt gewohnt ist“, sagt Chiang. Doch da sich dessen Hauptbestandteil Alit üblicherweise bei Temperaturen von 1250 Grad Celsius bildet und nicht elektrochemisch herzustellen war, musste Sublime schnell umdenken. Also machte sich das Team auf die Suche und entdeckte einen anderen Weg zu den chemischen Bindungen, die dem Portlandzement seine Festigkeit verleihen. Er beginnt mit der Wahl des Ausgangsmaterials: Statt Kalkstein nutzt Sublime „reichlich vorhandene carbonat-freie Gesteine und industrielle Abfälle“, wie es auf seiner Webseite schreibt. Infrage kämen etwa zerkleinerter Alt-Beton oder andere kalziumhaltige Gesteine wie Gips, Anhydrid oder die unterschiedlichen Feldspäte. Als Nebenprodukt fallen dabei oft noch hochwertige Metalle wie Magnesium an, die sich weiterverkaufen lassen.
Der Sublime-Prozess besteht aus zwei Hauptschritten. Zunächst erzeugt es aus kalziumhaltigen Gesteinen elektrolytisch Löschkalk. Diesen vermischt es in einer Klinkermühle mit Sand und erhitzt das Gemisch – ähnlich wie beim herkömmlichen Klinkerprozess zur Zement-Herstellung, nur dass deutlich geringere Temperaturen notwendig sind. Bei wie viel Grad Celsius das Gemisch gebrannt werden muss, verrät Sublime allerdings nicht. Beim Erhitzen wird dem Löschkalk das Wasser entzogen, und es entsteht Brandkalk. Dieser verbindet sich dann – wie bei der konventionellen Zement-Herstellung – mit den Silikaten aus dem Sand zu Alit.
„Es ist auch nicht ein ’neuer‘ Zement“
Die Wahl der Zementchemie mag spitzfindig erscheinen. Aber in einer traditionellen Branche wie dem Baugewerbe, in der zudem jeder Cent zählt, könnte sie ein entscheidender Faktor dafür sein, welche Startups große Aufträge und Partnerschaften erhalten. „Ich denke, die Leute sind zu Recht skeptisch gegenüber einem neuen Zement“, sagt Ellis, bevor sie sich selbst unterbricht: „Nun, es ist auch nicht ein ’neuer‘ Zement.“ Soll heißen: Die Herstellung ist anders, das Endprodukt nicht. Ellis behauptet, dass das Material von Sublime genauso stark und haltbar sei wie herkömmlich hergestellter Portlandzement, wenn nicht sogar noch stärker. Es sei dennoch möglich, dass Bauherren zumindest anfangs zögern, sich von ihrem vertrauten Material zu trennen, sagt Lalit von Climate Imperative.
Davor muss Sublime jedoch noch die wohl größte Herausforderung bewältigen: Sein Material in den für große Bauprojekte erforderlichen Mengen herstellen. Moderne Zementanlagen produzieren in der Regel über eine Million Tonnen pro Jahr, die Pilotanlage von Sublime gerade einmal 100 Tonnen. Sie sei im Grunde „ein Zementwerk für Ameisen“, sagt Ellis.
Nächstes Ziel: Zehntausende Tonnen Zement pro Jahr
Sublime hat die Skalierung im Visier, und zwar schnell. Die nächste Stufe ist eine kommerzielle Demonstrationsanlage, die Zehntausende Tonnen Zement pro Jahr produzieren und Anfang 2026 in Betrieb gehen soll. „Das ist die Größe, bei der man für die Zementwelt nicht mehr unsichtbar ist“, sagt Ellis. Danach soll eine großtechnische Anlage mit einer branchenüblichen Kapazität von einer Million Tonnen pro Jahr folgen. Das Unternehmen überlegt noch, wo es diese Anlage bauen soll, hofft aber, sie um 2028 in Betrieb nehmen zu können.
Das Gründerduo von Sublime ist nicht naiv, was die bevorstehenden Herausforderungen angeht. „Die Gründung eines Zementunternehmens ist wahrscheinlich eine der schwierigsten, die man sich vorstellen kann“, sagt Ellis. „Es ist nicht nur technisch schwierig, sondern auch sehr kapitalintensiv. Es ist riesig. Und es ist nicht sexy … Jeder benutzt und besitzt Zement, aber man sieht es nicht.“
Doch die Lösung dieses unsichtbaren Problems könnte die Welt um uns herum verändern. Zement ist ein Gerüst unserer Gesellschaft, und die Bemühungen, es zu verändern, sind – trotz enormer Herausforderungen – von entscheidender Bedeutung für eine saubere Zukunft des Bauwesens.