E-Lkw brauchen riesige Akkus: Wie sie ein einfacher Trick deutlich leichter machen soll
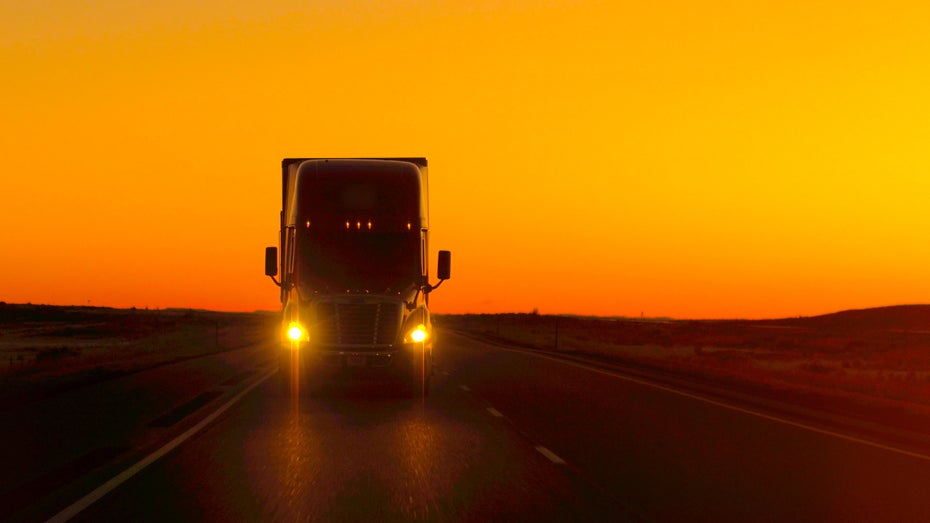
Warum sind Batterien eigentlich so groß und schwer? Zum Teil liegt das an ihrer aufwendigen Verpackung: Jede Zelle hat ihr eigenes Gehäuse; mehrere Zellen werden zu Modulen mit eigenen Gehäusen zusammengefasst; mehrere Module in einem weiteren Gehäuse ergeben eine Batterie. Diese Verschachtelung treibt Gewicht und Kosten in die Höhe. Ließe sich hier nicht deutlich einfacher Gewicht sparen als durch eine ausgeklügeltere Zellchemie? Genau das ist die Idee hinter dem „Cell-to-pack“-Verfahren. Dabei fallen die Module weg, und die Zellen werden direkt zu einer Batterie zusammengebaut.
Zwei „Cell-to-pack“-Ansätze im Vergleich
Pioniere dieses Verfahrens sind die beiden großen chinesischen Batteriehersteller BYD und CATL. Auf der Nutzfahrzeugmesse IAA konnte man die beiden Ansätze vergleichen. Der auffälligste Unterschied: Die Zellen der BYD-Tochter FinDreams sind sehr dünn, weniger als zwei Zentimeter. Nicht umsonst heißen sie „Blades“ (Klingen). Sie können lang und schmal ausfallen wie ein Stück Fußbodenlaminat, aber auch breit wie eine doppelte DIN-A4-Seite. Für eine flache Unterboden-Batterie werden dann beispielsweise mehr als hundert Zellen hintereinander gereiht. Bei CATL hingegen haben die sogenannten „Tianxing“-Zellen eher das Format alter Autoradios. Aber auch daraus lassen sich vergleichsweise flache Batterie-Packs zusammenbauen.
Die Energiedichte (auf Batterieebene) beträgt bei BYD rund 150 Wh/kg beziehungsweise 280 Wh/l. Das sei „15 bis 20 Prozent“ leichter als bei vergleichbaren Zellen in klassischer Modulbauweise, sagt Sabine Neff vom Zulieferer BorgWarner, der die Blade-Zellen außerhalb von China für Nutzfahrzeuge anbietet.
Die Gewichtsersparnis ist wichtig, weil praktisch alle Bus- und Lkw-Hersteller geschlossen auf Zellen aus Lithium-Eisenphosphat (LFP) setzen. Diese sind robuster und preiswerter als NMC-Zellen (Nickel-Mangan-Cobalt), wie sie in den meisten E-Autos arbeiten. Allerdings haben sie auch eine geringere Energiedichte. Dieses Problem lässt sich jetzt in einem gewissen Rahmen durch die Cell-to-Pack-Technologie kompensieren.
Wie es um das Recycling solcher Batterien steht
Eine offene Frage ist jedoch, wie es mit der Reparatur aussieht. Bei herkömmlichen Batterien lassen sich defekte Module austauschen. Für die einzelnen Zellen eines Packs ist das allerdings nicht vorgesehen – sie sind am Boden verklebt. „Die Batterien funktionieren aber auch noch, wenn ein paar Zellen ausfallen“, versichert Neff. Wenn es zu viele werden, muss die gesamte Batterie zum Recycler. Aber das Recycling selbst sei kein großes Problem, so Neff. Man sei schon mit einigen Betrieben in Gespräch.
Bis die Batterien wirklich geschreddert werden müssen, dürfte es eine Weile dauern. BYD und CATL versprechen für ihre Zellen eine Lebensdauer von rund 5000 bis 7000 Ladezyklen. Bei CATL können Kunden sogar wählen, was ihnen wichtiger ist: Hohe Energiedichte, schnelles Laden oder hohe Lebensdauer. Die „Long Life Edition“ beispielsweise bringt es laut Hersteller auf eine Lebensdauer von 15 Jahren beziehungsweise 2,8 Millionen Kilometern. Die CATL-Batterien sind bereits auf dem Markt; BorgWarner will die ersten Blade-Packs 2026 bei einem Bus einsetzen.