Akkutechnik: Diese Strategie verfolgen deutsche Autobauer im Kampf gegen Tesla
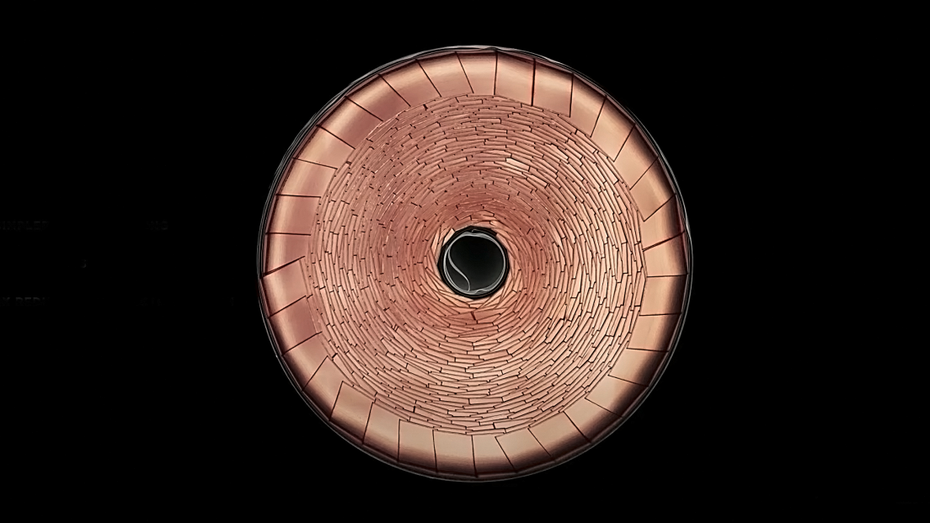
Mit schwarzer Jeans und T-Shirt liefern Musk und Mitstreiter einen Deep Dive in die elektrochemischen Feinheiten der Batteriefertigung. Auf dem Parkplatz neben einem Fabrikgebäude des Autobauers sitzen ein paar Hundert Tesla-Fahrer in ihren E-Autos, positioniert in Reih und Glied. 20 Millionen Fahrzeuge wolle er langfristig im Jahr herstellen, sagt Musk. Das sind doppelt so viele wie der gesamte Volkswagen-Konzern, der mit einem Dutzend Marken aufwartet. „Wir sind überzeugt, dass wir auf lange Sicht ein überzeugendes E-Auto zu einem Preis von 25.000 US-Dollar designen und herstellen können.“ Ein Hupkonzert bricht aus.
Schritt für Schritt erklärt Musk, wie er vor allem die Kosten für die teuren Batterien drücken will. 56 Prozent Einsparpotenzial verspricht er sich von neuartigen Batteriezellen, effizienteren Produktionsprozessen und alternativen Materialien, gefördert aus eigenen Minen in Nevada. Wie es angesichts dieser Visionen um die herkömmlichen Autobauer stünde, fragt ein Tesla-Fahrer in ein Mikrofon, das ihm durchs offene Fenster gereicht wird: „Wir sagen diesen Firmen: Hey, das müsst ihr auch machen, sonst werdet ihr in der Zukunft nicht mehr am Leben sein“, sagt Musk und schiebt lachend hinterher: „Aber weißt du was, sie glauben es einfach nicht.“ Und wieder: lautes Hupen.
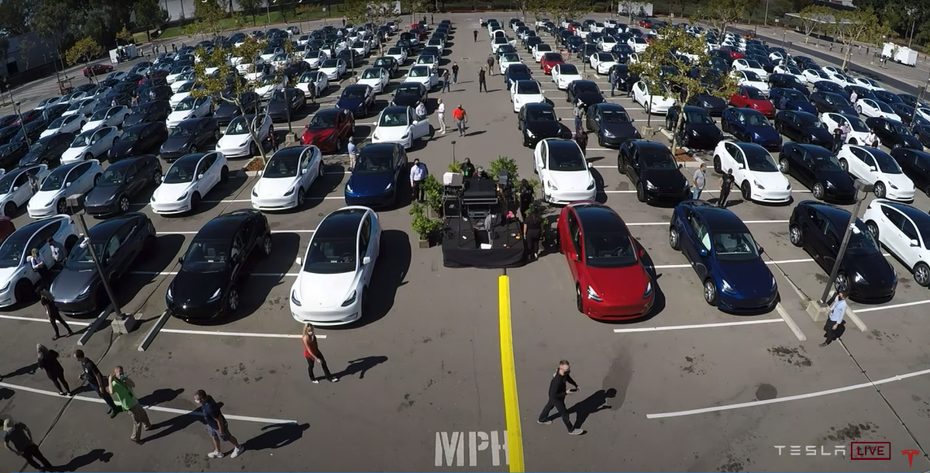
Beim Battery Day kam die Tesla-Community standesgemäß in E-Flitzern zusammen. Tesla-Chef Elon Musk kündigte an, langfristig E-Autos für 25.000 US-Dollar zu produzieren. (Abbildung: Tesla)
In den Berliner Ministerien dürften sie bereits vor Musks jüngster PR-Show nervös geworden sein, spätestens wohl, als er im November 2019 den Bau der Gigafactory ein paar Kilometer außerhalb der Hauptstadt ankündigte. Um den Automobilstandort Deutschland zu retten, macht die Bundesregierung knapp drei Milliarden Euro locker: „Das Herzstück jeder Batterie ist die Batteriezelle“, erklärt das Bundesministerium für Wirtschaft und Energie die Bereitstellung von Fördermitteln für Firmen und Forschung. „Für die Zukunft der Elektromobilität hierzulande ist daher die Ansiedlung einer Batteriezellfertigung in Deutschland und Europa ein bedeutendes wirtschafts- und industriepolitisches Thema.“
Darauf angesprungen ist jedoch nur der mittlerweile französische Hersteller Opel, der es am Werk in Kaiserslautern mit einer Zellfertigung versuchen will. Doch während selbst ein chinesischer Hersteller wie CATL eine Fabrik im thüringischen Erfurt hochzieht, wirken die Manager der deutschen Automobilfirmen erstaunlich gelassen. Derzeit betreiben weder der Volkswagen-Konzern noch Daimler, BMW oder deren deutsche Zulieferer nennenswerte eigene Zellfertigungen. Es würde reichen, die Details der Zelltechnologie zu verstehen, beteuern sie. Die Produktion überlasse man großen Herstellern und Startups, mit denen sich im Zweifel ja immer noch kooperieren ließe.
Muss im Fall enden, was nach Hochmut klingt? So abwegig ist deren Strategie gar nicht. Jetzt noch durchskalierten Produktionsprozessen der Lithium-Ionen-Batterie nachzueifern, sei ohnehin zu spät, empfehlen das Institut für Kraftfahrzeuge der RWTH Aachen und die Beratung Roland Berger dem Bundeswirtschaftsministerium: „Batteriewertschöpfung durch einen kurzfristigen, hochsubventionierten Aufbau einer wettbewerbsfähigen Massenproduktion von Batteriezellen zu sichern, wäre nicht zielgerichtet“, schreiben sie in einem Bericht. Grund zur Hoffnung gäbe es dennoch: Das Rennen um zukünftige Technologien, allen voran die der alternativen Festkörperbatterie, sei noch nicht gelaufen.
Es soll am Ende niemand sagen, keiner der deutschen Autobauer hätte es versucht. Daimler jedenfalls hatte sich in die Firma Li-Tec eingekauft, 2006 gegründet, noch bevor E-Mobilität die Schlagzeilen über die Branche beherrschte. Das Unternehmen lieferte Batteriezellen für die elektrische Variante vom Smart. 2015 beendete Daimler das Projekt jedoch wieder.
Vom Ausland abgehängt
Franz Nietfeld ist bereits seit fünfzehn Jahren bei Daimler Senior Manager für Battery Development. Seine Antworten formuliert der 55-Jährige grundsätzlich knapp, umso mehr jedoch, wenn er auf Li-Tec angesprochen wird. „Das Ganze ist ausgelaufen, obwohl die Technologien in der Leistungsfähigkeit absolut wettbewerbsfähig waren“, sagt er. „Für uns war das wirtschaftlich allerdings zu diesem Zeitpunkt so nicht darstellbar.“ Soll heißen: Andere konnten es billiger. Weiter kann er nicht in die Details gehen, betont jedoch immer wieder, dass das eine „sehr wertvolle Erfahrung“ gewesen sei.
Bei Daimler wissen sie nun, wie schwer es ist, den riesigen Playern aus Asien etwas entgegenzusetzen. Die erste sichere und fertigungsreife Lithium-Ionen-Batterie entwickelte der japanische Chemiker und spätere Nobelpreisträger Akira Yoshino bereits 1985, die ab 1990 von Sony serienmäßig in Camcordern und Walkmans, später in Handys und Laptops verbaut wurde. Samsung, Panasonic, LG Chem und zuletzt auch CATL spezialisierten sich auf die Technologie.
Je nach Anwendung experimentierten sie mit der Rohstoffzusammensetzung der beiden Elektroden. Da wäre die Anode auf der einen Seite. Sie ist aus Grafit und gibt beim Entladen Elektronen ab. Die gegenüberliegende Kathode, bestehend aus Kobalt, Nickel, Mangan oder Eisenionen, nimmt sie auf. Und umgekehrt beim Ladevorgang. Beide Elektroden sind mit flüssigen Elektrolyten getränkt, in dem sich Lithium-Ionen bewegen können. Daher auch der Name.
Über die Jahre haben die Hersteller die Produktionsprozesse, den Einkauf der Rohstoffe und den Vertrieb optimiert. Sie haben die Form, in der einzelne Batteriezellen zu Batteriepacks verschaltet werden, perfektioniert. Einzelne Zellen können dabei als zusammengerollte, zylindrische Batterien geformt werden wie bei Teslas ursprünglichem Partner – oder als gestapelte, rechteckige Kästen.
Natürlich weiß auch Nietfeld, wie zentral die Technologie für die Zukunft des Stuttgarter Automobilherstellers ist. „Die Zelle ist das Herz der Batterie“, wiederholt auch er das Mantra der Branche. „Das Ziel der Reichweite wird durch Fortschritte bei der Energiedichte erhöht“, sagt er. Ladezeiten, die Lebensdauer, Kosten, Leistung, Sicherheit und das Gewicht müssen bei zelltechnischem Design gegeneinander austariert werden. Das seien „wesentliche Faktoren für das Kundenverhalten“, sagt Nietfeld.
Die Zellen der Anderen
Und die Kontrolle über das „Herz“ gibt Daimler einfach den asiatischen Zulieferern in die Hand? Nietfeld widerspricht. Er verweist auf ein Zelltechnikum, das Daimler gegründet hat. Dort werde an Zellen geforscht. „Das Know-how bauen wir gemeinsam mit den Lieferanten auf“, sagt er. Sie hätten „Zugriff auf die neuesten Zelltechnologien“, würden diese künftig direkt von der thüringischen Produktionsstätte von CATL beziehen, diese erst in Kleinserien testen, später skalieren lassen und selbst weiterverarbeiten. Nach Kamenz, dem einstigen Standort von Li-Tec, lässt sich Daimlers Tochterfirma Accumotive die nötigen Einzelteile liefern, um daraus in zwei Fabriken Batterien zu produzieren.
Ferdinand Dudenhöffer kann das nachvollziehen. Autobauer seien schließlich keine Chemiekonzerne. Der ehemalige Professor der Universität Duisburg-Essen ist mittlerweile im Rentenalter, aber kommentiert als Direktor des CAR-Centers Automotive Research die Branche regelmäßig. Um Diplomatie kümmert er sich dabei heute noch weniger als früher. Berlin fördere „Mickey Mäuse“, meint er. „Jetzt noch Zellen selbst bauen?“, fragt er. „Da hat man eine so steile Lernkurve. Es ist wirklich schwierig, noch gegenzusteuern.“
Auch die anderen deutschen Autobauer stellen keine eigenen Batteriezellen her. Bei BMW nennen sie es „Kompetenzzentrum Batteriezelle“ und bei Volkswagen „Center of Excellence“: Forschungseinrichtungen, in denen an Prototypen gebastelt wird, deren Massenfertigung anschließend an Zulieferer ausgelagert wird. Mit Partnerschaften und Beteiligungen versucht man, diese näher an sich heranzuholen. So investierte Volkswagen in den schwedischen Batteriehersteller Northvolt, der im niedersächsischen Salzgitter eine Batteriezellenproduktion hochziehen will.
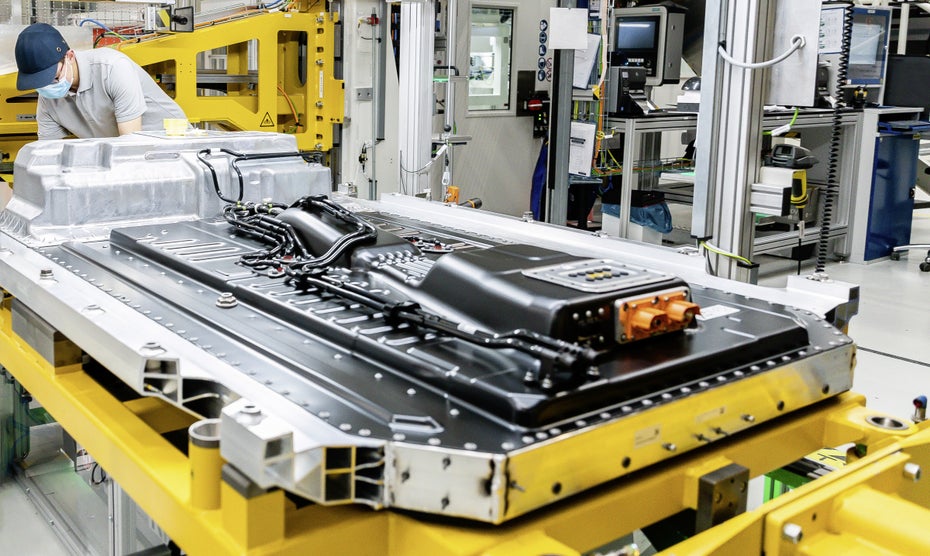
Die Daimler-Tochter Accumotive lässt sich von Zulieferern die Bauteile für die Lithium-Ionen-Batterien liefern und baut sie selbst nur noch zusammen. (Foto: Mercedes-Benz / Accumotive)
Einzig der Premiumhersteller Porsche, ebenfalls Teil des Volkswagen-Konzerns, habe ein deutsches Startup ausgemacht, um eine Batteriezellenfertigung zu starten: Customcells, 2012 aus einem Fraunhofer-Institut im schleswig-holsteinischen Itzehoe ausgegründet. „Gerüchte“ nennt ein Sprecher bei Porsche einen Bericht des Tagesspiegels und will das nicht weiter kommentieren. Auch bei Customcells will sich niemand zu dem angeblichen Vorhaben äußern. Solange das Thema ausgeklammert werde, sei Benno Leuthner, Head of Project Planning & Sales, allerdings gerne bereit für ein Videointerview.
Mit schwarzem Pullover – und mit sicherem Abstand zu seinem Pressesprecher – sitzt der 37-Jährige in einem weißen Konferenzraum. Homeoffice ist für ihn schwer umsetzbar, weil der gelernte Maschinenbauer sich bei den Fachleuten in den Laborräumen immer wieder nach dem neuesten Stand erkundigt und interessierte Gäste durchs Gebäude führt, darunter Chemiefirmen, Autobauer und Batterieproduzenten.
Mehr als 250 Rohmaterialien haben sie auf Lager, um an der optimalen Batteriezelle zu tüfteln. „Natürlich hatten wir immer das Interesse, mit unserer Technologie in die Elektromobilität zu gehen“, sagt Leuthner. Ihre Produkte würden sie jedoch auch anderen Branchen anbieten, beispielsweise Drohnenherstellern, der Medizintechnik und der Schifffahrt.
„Jetzt noch Zellen selbst bauen? Da hat man eine so steile Lernkurve.“
Von Anfang an ging es ihnen um konkrete Anwendungen. Dabei entwickelten sie in Kleinserie, sagt Leuthner. „Unsere Kunden schätzen, dass sie die Zellen individuell an ihre Bedürfnisse anpassen können. In Tübingen hat Customcells dafür eine Fertigungshalle errichtet, in der 30 der insgesamt 100 Mitarbeiter tätig sind. Es sind die Feinheiten für die perfekte Performance, die Autobauer mit Customcells durchspielen können. Mit einer Gigafactory habe das nichts zu tun. „Der große Massenmarkt steht für uns als Nischenanbieter im Bereich des Prototypings nicht im Fokus“, erklärt er.
Ob die Kleinserienproduktion das unabwendbare Schicksal deutscher Zellenhersteller sei, verneint Leuthner dennoch: „Grundsätzlich gibt es am Standort Deutschland gute Rahmenbedingungen für den Aufbau einer Serienfertigung jeglicher Größenordnung“, sagt er. Wer diese Rolle eines Tages übernehmen könnte, bleibt offen.
Skalierung hin oder her: Es bleiben die Zweifel, ob das überhaupt lohnenswert wäre. Autoexperte Dudenhöffer hält die Zahlen für irreführend, mit denen der Bundeswirtschaftsminister für die heimische Zellproduktion wirbt. Altmaier zufolge würden 40 Prozent der Wertschöpfung der Batterie auf die Zelle entfallen. Der Herstellungsprozess der Zellen betrage jedoch nur 15 Prozent, will Dudenhöffer berechnet haben. „Die Produktion selbst ist kein Unterscheidungsmerkmal“, sagt er. „Nicht die Zellproduktion, sondern das Material für Kathode, Anode und Elektrolyt macht die Speicherfähigkeit aus.“ 65 Prozent der Wertschöpfung würden auf das entsprechende Zellmaterial der Kathode entfallen, weitere 25 Prozent auf das der Anode.
Elon Musk sieht das anders. Bei seinem Ziel, die Kosten zu senken, krempelt er auch Produktionsprozesse um, will möglichst alles unter seine Kontrolle bringen. „Auch Tesla wird in Zukunft nicht alles selber machen können“, winkt Dudenhöffer ab. Die gewohnte Arbeitsteilung zwischen deutschen Autobauern und Zulieferern hält er nicht für überholt.
Blöd nur, dass Continental und Bosch keine Chancen sehen, so spät noch in das Geschäft mit Zellen einzusteigen. Nur der Chemiekonzern BASF versucht sich mit Fördermitteln des Bundes an der Fertigung von Zellmaterialien. Der Batteriehersteller Varta erhält ebenfalls Gelder – will allerdings keine Zellen für E-Autos entwickeln, sondern für kleinere Elektronik wie Wearables, so ein Sprecher.
Im Bundesministerium für Wissenschaft und Forschung hoffen sie, noch eine Abkürzung für die deutsche Autobranche gefunden zu haben. „Es gibt den Wunsch, mit einer neuen Technologie ganz vorne mitspielen zu können“, sagt Helmut Ehrenberg, Professor am Karlsruher Institut für Technologie, Fachbereich Angewandte Materialien. Er ist im Homeoffice zu erreichen. Ins Labor muss er kaum noch in seiner koordinierenden Rolle als einer der Verantwortlichen in einem Verbundprojekt zwischen Helmholtz-Instituten, der Fraunhofer-Gesellschaft und Universitäten in Gießen und Marburg. Mit gebündelten Kräften sollen sie die Entwicklung der sogenannten Feststoffbatterie vorantreiben. Mit 3,7 Millionen Euro wird das „Festbatt“-Cluster über drei Jahre gefördert.
Instabil und Leicht Entzündlich
So weit die Lithium-Ionen-Batterie auch verbreitet ist, sie ist alles andere als perfekt. „Der Flüssigelektrolyt, das ist der Flaschenhals“, formuliert es Ehrenberg. Beim ersten Laden gebe es eine chemische Nebenreaktion – und 20 Prozent der Kapazität seien futsch. Zudem sei der flüssige Elektrolyt leicht entzündlich, weshalb die Entwickler peinlichst darauf achten müssten, die Leistungsdichte nicht so hochzufahren, dass die Sicherheit darunter leide. „Die logische Konsequenz ist, die brennbare Flüssigkeit, die organische Komponenten enthält, durch eine Keramik zu ersetzen“, beschreibt Ehrenberg.
In der Anfangsphase ging es ihnen jedoch erst einmal darum, überhaupt in größeren Mengen an die nötigen Festelektrolyte zu kommen. Jetzt testen sie grundsätzliche Eigenschaften der Materialien. Und sogleich wieder ein Dämpfer: Auch bei den neuen Stoffen kommt es zu ungewollten chemischen Reaktionen. „Flüssige Elektroden sind instabil, Keramik per se stabil – so einfach ist es leider nicht“, sagt er. Noch ist offen, ob sie das in den Griff bekommen werden. „Es gibt keine Garantie, dass man damit jemals in Serienfertigung gehen kann“, betont Ehrenberg.
Wenn alles glatt läuft, geht das Forschungscluster im kommenden Jahr in die zweite Runde. „Aber auch Festbatt II wird keine fertige Batterie auf den Tisch legen.“ – Ehrenberg will die möglichen Erkenntnisse dennoch nicht kleinreden. Es wird regelmäßig ein „Managementkreis“ mit Experten aus den führenden Firmen der Branche einberufen, um die Fortschritte zu diskutieren. Manche hoffen, dieses Mal früher vorne mit dabei zu sein. Volkswagen beispielsweise hat 2018 in Quantumscape 100 Millionen US-Dollar investiert, ein US-amerikanisches Batterie-Startup, das die Massenproduktion von Festkörperbatterien vorbereiten will.
Die Festkörperbatterie bleibt fern
„Für die Zukunft wird erwartet, dass die Festkörperbatterie die Reichweite deutlich erhöhen und die Ladedauer weiter verringern wird“, hat Volkswagen einen weiteren Zuschuss von 200 Millionen US-Dollar in diesem Jahr begründet. Auf die Frage nach der Einsatzbereitschaft der neuartigen Batterie antwortet Frank Blome, Leiter des Center of Excellence Batteriezelle: „Zwischen 2025 und 2030 könnte es so weit sein.“
Selbst wenn der Durchbruch gelingen sollte: Womöglich würde dieser abermals nicht hierzulande stattfinden. Toyota habe anlässlich der diesjährigen Olympischen Spiele einen schnuckeligen Shuttle-Bus vorstellen wollen, angetrieben durch eine Festkörperbatterie. Dann kam Covid-19 dazwischen. Ehrenberg muss lachen, als er davon erzählt, für so unglaubwürdig hält er den angeblichen Coup. Vielleicht schwingt da aber auch etwas Nervosität mit. „Weiter zu verfolgen, was andere schon geschützt haben, ist wettbewerbstechnisch natürlich wertlos“, sagt er über Patente, an denen hinter den verschlossenen Türen asiatischer Entwicklungslabore geschrieben werden könnte.
Fehlt eigentlich nur noch, dass auch Elon Musk den Einstieg in die Technologie verkündet. Bislang blieb der jedoch bei vagen Sympathiebekundungen, mehr nicht. Außerdem: Noch ließen sich aus Lithium-Ionen-Zellen massive Verbesserungen herausholen, hat Musk im kalifornischen Fermont immer wieder betont.
Und für ausreichend Nervosität bei der Konkurrenz dürfte er zwei Wochen danach mit seinem Tweet ohnehin gesorgt haben. Für die Serienfertigung der frisch designten Batteriezelle, der „4680 tabless cell“, gäbe es bereits einen Standort: Berlin-Brandenburg.
Blöd nur, dass diverese Unternehmen bereits Autos von Tesla außeinandergebaut und analysiert haben, und dabei dann herauskam, dass durch mehr in-house sich viele Vorteile ergeben.. Aber ja, Zulieferer sind das beste das es gibt .. total flexibel ….