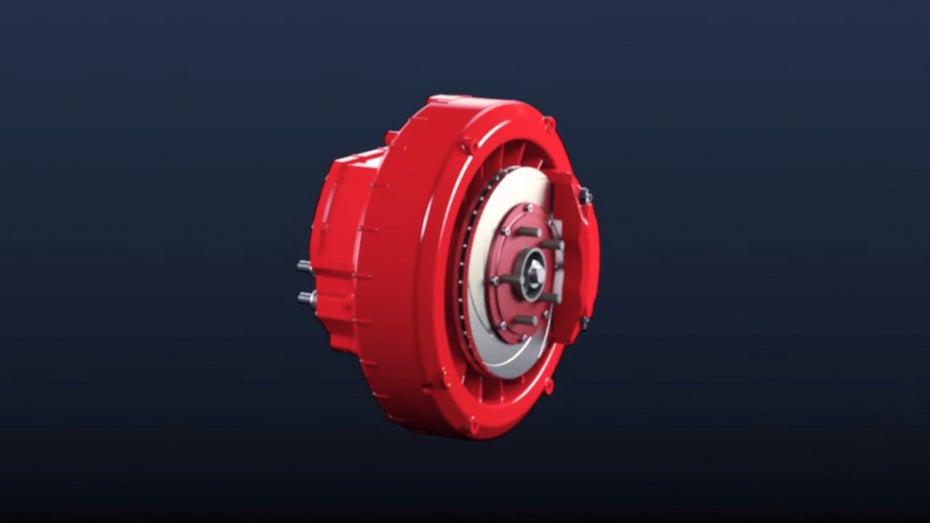
Hitachi hat sich an der Technik des Radnabenmotors versucht. Sie ist über 120 Jahre alt. (Bild: Hitachi)
Der Radnabenmotor ist zurück. Das gilt schon länger und immer wieder. Jetzt haben der japanische Hersteller Hitachi und seine Partner den „In-Wheel-Antrieb“ – so heißt diese Motorart im 21. Jahrhundert – weiterentwickelt. Das neue Konzept hat einiges für sich: Es vereint Motor, Wechselrichter und Bremse. Das Ganze soll am Ende in eine 19-Zoll-Felge passen. Es ist das erste Produkt des Joint Ventures Hitachi Astemo (Astemo steht für „Advanced Sustainable Technologies for Mobility“; auf Deutsch „Fortschrittliche nachhaltige Technologien für Mobilität“), das mit der Erfindung nun auf dem 30. Aachener Kolloquium an die Öffentlichkeit ging. Die neue, alte Technologie hat jedoch auch Nachteile.
Radnaben-Porsche-Sensation auf Weltausstellung
Schon vor 120 Jahren hat Ferdinand Porsche elektrische Radnabenmotoren entwickelt und beim „Lohner-Porsche“ eingesetzt. Die Sensation zeigte er als ersten transmissionslosen Wagen auf der Weltausstellung 1900. Lohners Grund für die elektrischen Fahrzeuge: Die Luft werde von in großer Anzahl auftretenden Benzinmotoren „erbarmungslos verdorben“. Hitachi Astemos Ansatz geht weiter: Ihr Radnabenmotor soll den Energieverlust von herkömmlichen Elektromotoren um 30 Prozent reduzieren.
Masse und Gewicht entscheidend für den Direktantrieb
Die Technologie setzte sich aufgrund ihrer Nachteile nie wirklich durch, auch wenn Wasserstoff-Busse mit Radnabenmotoren herumfahren und Elektroauto-Startups es wieder damit versuchten. Problem Nummer 1: Die ungefederten Massen steigen stark. Das ist das Gewicht, das direkt auf die Achsaufhängung einwirkt. Es hat hohen Einfluss auf den Federungskomfort gerade bei höheren Geschwindigkeiten und fällt daher bei Stadtbussen nicht so stark ins Gewicht. Hitachi Astemo will mit einem besonders leichten Design den Zuwachs an ungefederten Massen „erheblich begrenzt“ haben. Unter anderem soll das Strahlschweißen in der Fertigung dabei helfen.
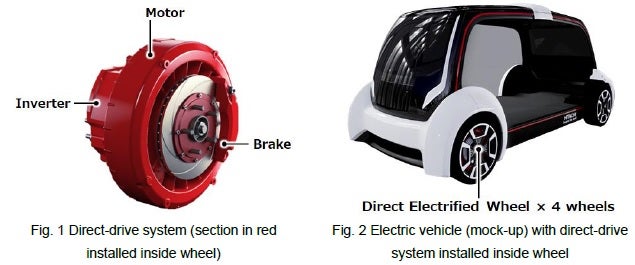
Der neue Motor vereint Antrieb, Bremse und Inverter in einem. (Bilder: Hitachi)
Weniger Raum durch höhere Kühlung
Das zweite Problem heißt Kühlung. Gerade bei hoher Belastung entsteht dieser kompakten Bauform daraus eine Herausforderung. Eine „Direct-Cooling-Technologie“, bei der hochisolierendes Kühlöl die Halbleiter und Spulen umspült, soll die Komprimierung des Bauraums möglich machen. Das japanische Konsortium schreibt, durch das Design erfordere der „Direct-Drive-Motor“ kaum Änderungen bei der Aufhängung und anderer Konfigurationen. Sprich: Die Hersteller sollen ihre Standard-Aggregate recht einfach ersetzen können.
240 Kilowatt maximale Systemleistung
Um die Leistung zu erhöhen, hat Hitachi die Anzahl der Magnetpole erhöht und den magnetischen Fluss pro Pol optimiert. Der Direct Drive besitzt nun eine Leistungsdichte von 2,5 Kilowatt pro Kilogramm. Maximal leiste er 60 Kilowatt pro Einheit, heißt es. Bei einem Allradantrieb ständen demnach 240 Kilowatt Systemleistung zur Verfügung. Das maximale Drehmoment gibt das Unternehmen mit 960 Newtonmeter an. 420 Volt Spannung benötigt der Antrieb und kann eine Stromstärke von bis zu 280 Ampere verarbeiten.